Découvrez le concept du TPM, ses 8 piliers historiques et comment ils contribuent à améliorer les rendements de vos équipements de production. Mais aussi comment KLMANAGEMENT vous accompagne pour initier une telle démarche avec son offre Reboost TPM.
Qu’est ce que Total Productive Maintenance ?
Le Total Productive Maintenance est né en 1971 à l’initiative de Nippon Denso. Mais il n’a connu un décollage qu’en 1984 suite à la formalisation par le Japan Institute of Plant Maintenance.
Dans les années 70, le Japon était d’une part en plein déploiement du Just in Time. Et d’autre part en plein développement de mécanisation et d’automatisation. Mais aussi à la croissance du développement rapide du renouvellement de gammes de produits sur les marchés. Les trois environnements demandaient plus de fiabilité aux machines et plus de réactivité devant les aléas.
Les structures traditionnelles de maintenance et de production (chacun chez soi) étaient incapables de répondre à ces nouveaux besoins. Elles devaient donc évoluer.
Le Total Productive Maintenance était essentiellement centré sur la machine et sa productivité. Celle-ci, mesurée avec le fameux TRS, met le focus sur la réduction des pertes. L’arrivée tonitruante du Lean, avec ses 7 muda, a poussé à élargir la cible du Total Productive Maintenance. La présentation des 16 pertes en production a élargi les domaines d’action et fait du Total Productive Maintenance un modèle de management de la performance en production.
Voici comment Nakajima, père du Total Productive Maintenance, le définissait :
La Total Productive Maintenance :
- A pour objectif la réalisation du rendement global maximum de l’équipement
- En cherchant à établir un système global de maintenance productive pour toute la durée de vie des installations
- Et ce en impliquant la participation de toutes les divisions notamment celles de la conception, de l’exploitation et de la maintenance
- A tous les niveaux hiérarchiques, des Dirigeants aux Opérateurs
- Tout en établissant comme moyens de motivation, les activités autonomes du personnel regroupé en cercles
Seiichi Nakajima
Les 8 piliers de la TPM
Ces 8 piliers constituent l’armature technique de TPM. Ils illustrent concrètement ce que la méthodologie à la japonaise veut dire. Des emprunts sont faits au TQC (Total Quality Control), le 5S est intégré dès le démarrage du programme TPM comme une sorte de pré requis et comme trame méthodologique pour les activités d’inspection de la maintenance autonome. Ces intégrations de pratiques et de méthodes visualisent l’intégration de la TPM dans son environnement de production.
Comme le disait Nakajima « Sans TPM effectif, pas de JIT qui marche et pas de TPS qui fonctionne ».
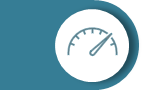
TRS et la réduction des pertes
Il s’agit de réduire les 16 pertes de production par des activités d’amélioration (Kaizen). Les premières applications sont faites sur les bottelnecks dans leur ligne. Et elles servent de démonstrateurs pour les résultats attendus et pour les méthodes à appliquer.
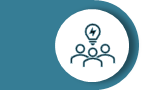
Maintenance Autonome
C’est la prise en charge par la production, et plus concrètement par l’opérateur de fabrication, de la maintenance des équipements. C’est aussi développer l’autonomie au poste de travail pour rendre l’opérateur moins passif et moins dépendant. On retrouve deux types d’activité dans la maintenance autonome. D’une part, les routines quotidiennes et d’autre part le traitement des aléas. La mise en place de la maintenance autonome fait l’objet d’une méthode spécifique en 7 étapes.
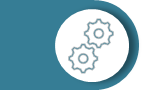
Maintenance Programmée
C’est la partie technique de la maintenance dans ses différents niveaux : le curatif, le préventif et le prédictif. La Maintenance Programmée propose des méthodes pour établir un programme de maintenance planifiée. Au-delà de la technique maintenance, TPM prend en charge la gestion du stock de pièces de rechange, le contrôle et l’amélioration des coûts de maintenance ainsi que l’augmentation de la durée de vie des pièces et des équipements.
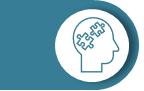
Développement des compétences
L’objectif ici est d'accroître les compétences des opérateurs en production comme des opérateurs de maintenance via trois canaux. Le « OJT »(On the Job Training) est un moyen de formation important : des formes de monitorat permettent aux meilleurs opérateurs de démontrer leur pratique lors des interventions réelles. La pratique du « dojo » est un second canal de formation. Les connaissances de base, comme les nouvelles données liées aux spécialisations, sont diffusées sur un mode classique de stages, diffusés dans l’entreprise ou en milieu académique extérieur.
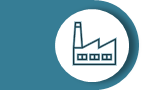
Management initial des installations
L’approche ici est double. D’une part, il s'agit de vérifier que les nouveaux produits ne génèrent pas de difficulté de réalisation aux différents stades de leur process global, pour les corriger avant lancement en production. Et d’autre part en intégrant dans les nouveaux équipements les améliorations issues de l’analyse du passé et vérifier que les capabilités soient cohérentes avec les besoins du produit. On retrouve là les notions d’AMDEC, de Life Cycle Costing pour l’essentiel. L’objectif est d’assurer des démarrages en production les plus rapides possible et des « vertical ramp up ».
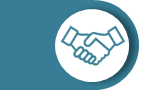
Management qualité produit et service client
L’objectif est de réduire à zéro les défauts sur le produit. L’entrée dans le problème est le défaut produit : l’élargissement des causes au-delà de l’équipement, permet d’installer une cohérence entre les différents systèmes de standards du contrôle qualité, du système de maintenance, à la fois sur l’interne et à la fois avec les fournisseurs.
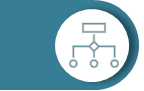
Optimisation des activités supports
Deux axes de travail dans ce pilier : développer les contributions des « services » aux activités TPM en production et conduire les améliorations dans son propre secteur, telles que 5S, office sans papier. Il n’est pas envisageable de demander des ateliers propres et rationnellement « rangés » en production, si on laisse se développer le « bazar » dans les services périphériques et les ateliers de maintenance.
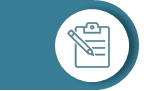
Santé, sécurité et environnement
C’est le domaine du zéro accident et zéro pollution. C’est une démarche de sécurité classique : analyser les accidents et les risques pour en éradiquer les causes potentielles.
L’approche Reboost TPM de KLMANAGEMENT
La valeur ajoutée du programme réside autour de 3 focus clés pour ancrer les pratiques et enjeux de TPM tout en incluant les problématiques de l’usine du futur (TPM 4.0).

Nos domaines d’expertises
Lorsque leurs enjeux de transformation sont identifiés, nos clients font appel à notre expertise pour les accompagner dans la construction et l’exécution de leur programme d’amélioration de la performance.